13/07/07
The world's first commercially available module-building cotton
harvester rolled off the manufacturing line this week. The machine
is the Case IH Module Express 625, which allows growers to save
capital, fuel and labour by combining cotton harvesting and module
building in a single operation. This cutting-edge technology will
be available to growers in time for this fall's harvest.
Minnesota Gov. Tim Pawlenty took the wheel of the world’s
first module-building cotton picker when it rolled off the manufacturing
line in Benson, Minn. on July 11, 2007. The huge machine, the Case
IH Module Express 625, saves fuel, labour and capital for cotton
growers.
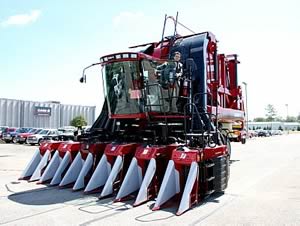 |
The new machine continues a Case IH tradition of cutting-edge
cotton technology. In 1943 the company introduced the first commercially
successful mechanical cotton picker, the H-10-H. The original machine,
known as "Old Red," has been donated to the Smithsonian
Institution and named a landmark of agricultural engineering by
the American Society of Agricultural Engineers.
Industry benefits
Like its predecessor "Old Red" the Case IH Module Express
has the potential to transform the cotton industry, because it's
designed to fit the needs of ginners as well as growers, says Trent
Haggard, Case IH marketing manager for cotton harvesting.
"In the development process, we listened to input from the
industry. Our engineers made sure that the Module Express fit with
existing cotton production practices, with no additional handling,
logistics or costs," Haggard says. "That's especially
important when you consider that many of today's cotton growers
are also gin shareholders."
Case IH began testing various concepts for a module-building cotton
picker in the 1970s, including configurations that produced round
bales and smaller rectangular modules.
"The overwhelming favorite concept of ginners and farmers
alike was an 8-foot by 8-foot by 16-foot module, which is exactly
half the size of traditional modules. That means that gins can
handle our modules with zero additional investment.
"Ginning Case IH modules and traditional modules together
is a seamless operation. A modern cotton gin that produces 60 ginned
bales per hour will be equally maximized while ginning the Case
IH module," Haggard says.
Cost savings for growers
With the Module Express, a single machine does the work that previously
required a picker, a boll buggy and a tractor to pull the cotton
to a separate module builder operated by another tractor. That
means operators can reduce their investment in fuel, labor and
capital. Cost savings with the Module Express total 25 percent
compared to traditional cotton harvesting methods, according to
a study by Mississippi State University economist D.W. Parvin.
"With this equipment you can cut your labor force by more
than half. It makes life a lot easier," says Jimmy Hargett,
who field-tested four Module Express units on his farm near Memphis,
Tenn.
No plastic or twine contaminants
The Case IH Module Express utilizes an environmentally friendly,
16-foot tarp to protect bales from weather damage. Tarps are made
of a reusable material to eliminate the risk of contaminating the
finished product. If twine or plastic enter the harvest or module
building system, it can be ingested into the cotton gin and even
woven into the dyed cotton, resulting in a defective garment.
"For environmental reasons, we appreciate not having to use
disposable plastic covers on the modules," says Kenneth Hood,
past president of the National Cotton Council and a farmer and
ginner in Gunnison, Miss.
"Besides avoiding potential contamination, the reusable tarps
are durable and cost-effective. They can be used up to five times
per season and last up to seven years, resulting in a low cost
of 31 cents or less per ginned bale," Haggard adds.
In-field advantages
The Module Express offers productivity advantages in the field,
too. Compared to a traditional module, the Case IH module is not
pressed into the ground. The densely packed module can be loaded
into the truck more easily, with minimal waste.
Full modules can be unloaded either at the end-row or elsewhere
in the field, depending on the operator's needs and the size of
the field. "In 60 to 70 percent of fields, operators will
be able to leave ready-to-load modules at the end-row, to be picked
up by a module truck with no need for a mover," says Haggard.
Designed with optimal traction and flotation characteristics, the
Module Express harvests just as effectively on wet or dry ground.
The machine has a longer wheelbase than most traditional pickers,
giving it optimum front-to-rear machine balance. Low-inflation
front dual tires and large steering tires leave a minimal footprint
in the row. Yet, the 365-hp Module Express has plenty of heft with
a 9-liter powerplant and an all-wheel-drive powertrain.
Because it picks cotton from both sides of the row, the Module
Express also harvests more cotton with each pass. For a custom
operator like Darryl Pasket of Anderson, Tex., that means more
money on his bottom line.
"The Module Express picks the field cleaner. When you're paid
by the lint pound, the added productivity of the machine makes
a big difference," Pasket says.
Yet these productivity gains don't add maintenance, Haggard points
out. "The engineers at Case IH added functionality without
requiring additional service and maintenance points. The new machine
actually requires less maintenance than a traditional basket picker."
Award-winning designs
Production of the Module Express 625 comes on the heels of two
recent design awards from the American Society of Agricultural
and Biological Engineers (ASABE). The Module Express 625 was recognized
last month with ASABE's AE50 award for engineering excellence.
The AFS Cotton Yield Monitor, an option on the cotton picker, also
received an AE50 award. The awards are based on commercial impact,
contributions to agriculture and technological significance.
"Case IH has a legacy of innovation in cotton harvesting,
starting with the first commercial cotton picker in 1943. We're
pleased to be able to continue our company's tradition of industry-leading
technology by delivering the Module Express 625 to today's cotton
growers," concludes Haggard.
Claas Xerion Tractor Passes Endurance Test
AGCO Confident in Laverda
AGCO Corporation Takes Stake in Laverda
Multi-Purpose Handler from Landini is a Versatile Power Unit
|