22/08/07
A NEW initiative designed to help dairy farmers cut their energy
costs for milking and milk cooling is to form a key focus for milking
parlour and milk tank experts Fullwood at this year’s Dairy
Event (stand number EH2 - 236, 19 and 20 September 2007, Stoneleigh
Park, Warwickshire).
Fullwood milk tank
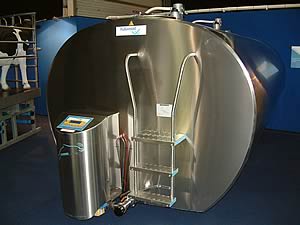 |
Based around a number of cost saving components that the company
is launching or has developed, the initiative also seeks to help
reduce carbon emissions.
“Electricity consumption is a major contributor to the costs
of running a dairy farm,” explains Fullwood technical director,
John Baines.
“Typically, electricity costs in a parlour and dairy are
split into three parts: one third for running the vacuum pump in
the parlour; one third for heating water for washing; and one third
for milk cooling. We are focused on helping producers make savings
in all three of these areas, with plans to launch several new energy-saving
components on the stand.”
Assessing vacuum costs first, Mr Baines says for most of the time
during milking, full operation of the vacuum pump isn’t required.
Full capacity is required during washing, he says, but once milking
has started, full vacuum reserve may only be needed when clusters
are attached or kicked off.
With the new Fullwood vacuum sensor and speed controller unit designed
for fitting to vacuum pumps, pump capacity is only made available
as and when needed. In this way, it has the potential to more than
halve electricity costs for running the vacuum pump, estimates
Mr Baines.
“The new sensor and speed controller will be exhibited in
conjunction with a new high capacity pump which we are also launching
on the Dairy Event stand,” he points out.
To help reduce water heating costs, the company is also exhibiting
its new heat recovery unit – which re-cycles heat emitted
from the compressor on the milk refrigeration unit and uses this
to heat water for washing.
“On one farm, water reached 62 degrees C where the heat recovery
unit was used. Based on an ambient water temperature of 15 degrees
C, this equates to 47 degrees out of the total 75 uplift normally
needed to heat water to 90 degrees C. In other words, over 60%
of the energy needed could be provided by the heat recovery unit
alone.”
For milk cooling, with rising energy costs, Mr Baines says now
is the time for producers to reconsider ice bank tanks. These use
cheap rate electricity to build up a store of ice which is used
to cool milk later as a way of making savings, rather than drawing
on electricity during peak times. “By spreading electricity
consumption over the day, farmers can reduce peak demand and may
be able to access cheaper tariffs.
“All three of these areas are part of our drive to help farmers
lower their cost of ownership of milking parlours and bulk tanks.
These include savings on energy but also savings on items such
as ease of cleaning, which we are tackling with other parlour developments” he
adds.
Capital Milk to Buy and Sell Milk on Behalf of UK Dairy Farmers
New Research Reveals Opportunities for Dairy with Provenance
New Fullwood Milking Parlour Design Offers Hygiene Boost |