12/06/06
Upgrading to automatic, unmanned batch grain drying has produced
a number of significant advantages on a Cumbrian farm.
James Taylor and his grain dryer
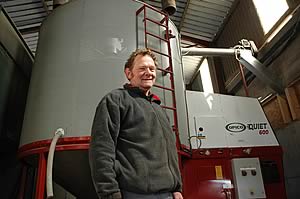 |
Labour has been freed up to get on with other vital harvest tasks,
such as baling, while the machine’s quiet operation enables
drying to continue during the night if necessary.
The family farming partnership of J & J & D Taylor, English
Town Farm, Longtown, Carlisle, purchased an OPICO 600QF batch dryer
in time for the 2004 harvest and two seasons’ use has convinced
them that they made the right decision.
James Taylor, who farms with his brother John and wife Doreen,
estimates that the dryer handles about 700 tons of grain a year.
“We had an OPICO mobile dryer previously and one of the
reasons for getting another one was its mobility,” said Mr
Taylor. “This allows us to move it about if we change
our storage and drying policy. We did this with the previous dryer,
which gave us some flexibility.”
However, compared to their previous dyer, which was tractor-driven
and manually operated, the new automatic model is much easier to
control, said Mr Taylor. “It does precisely what you ask
of it. It’s allowed us to do more batches in a day
because we’ve more control over the whole operation.”
Of the farm’s 660 acres, some 300 acres are arable - mainly
spring barley, plus winter triticale and some oil seed rape. The
remaining acreage is grassland supporting suckler cows and sheep.
The soil type varies, from light land with sand and gravel, to
heavy clay and peat moss.
A plus factor for buying the OPICO dryer was the trade in price
Mr Taylor received for the old model. “A mobile dryer
has a far higher second-hand value than a static system, simply
because there’s no installation involved,” he said.
There was another major consideration at the time of purchase,
he added. “We only have single-phase electricity here. So
at harvest time we hire a self-contained diesel generator from
a local plant hire company to drive the dryer. We would have had
to do the same with a static system, but with this machine it’s
just one cable into a generator and away you go. You could virtually
dry in the middle of a field if you had to.”
The first season they had the dryer, they hired a generator for
four weeks. “In 2005 we tried to save on hire charges and
managed to condense it into two weeks. Partly this was because
the harvest was a bit drier, so the grain dryer didn’t need
to do so much work.
“We also put in three or four days combining before we started
to dry to reduce the generator hire period. We were finished by
the end of August.”
The dryer is housed under cover in the grain store, and its quiet
operation is an asset. “The grain store is in close proximity
to the house, but it doesn’t cause any problems.
“With it being electric and automatic, it allows us to dry
a lot more at night when the temperature’s cooler.”
Just to the side of the dryer is a holding bin with a capacity
of 14-15 tons, equipped with a telescopic loader. “It’s
a tidy, compact outfit, totally self-contained, with the minimum
of conveying,” said Mr Taylor. “Whenever there’s
someone in with a load of grain off the combine, we just keep topping
it up.
“Its important to have a holding bin so that as soon as
the dryer has discharged the dried grain, it goes on to fill itself
again.”
Some of the grain is for home consumption, while the balance is
sold through local farmers’ co-operative, Northern Grain.
As far as the finished product is concerned, Mr Taylor is impressed. “The
grain sample is significantly improved through the polishing effect
of continuous recirculation”, he said. “We use
the screen in the auger like a pre-cleaner and its amazing the
amount of lights and small grains that are cleaned out of the sample.”
Opico designed for grassland success
Case IH And Ferrari To Share Spotlight At Grand Prix Events in Canada and U.S.
Pecks AgriTrac investing in Case IH
Case IH at Grassland 2006
|